Single-layer indium tin oxide (SITO) touch solutions will sweep the mobile phone market this year. Mainland China's first- and second-tier brand factories and white-label manufacturers are working hard to sprint into the mid-to-low-priced smartphone market. Therefore, the cost requirements for touch panels have become increasingly stringent, driving single-layer indium tin oxide (SITO) transparent conductive Demand for shipment of touch solutions based on film structures has surged. At present, touch chip and module manufacturers are competing to expand production. It is estimated that the penetration rate of SITO touch panels in the mobile phone market will reach more than 70% this year.
At the same time, the position of in-cell touch solutions in the high-end mobile phone market will also become more stable. As chip makers and panel makers have worked together to develop In-cell touch panels with high production yields and plan to expand production in the second half of this year, they will gradually relieve the doubts that In-cell has insufficient capacity and high costs. In turn, it will attract more mobile phone brand manufacturers to accelerate the introduction of this solution in a new generation of high-end products.
Mid- and low-priced mobile phones lift SITO touch soaring value
Bai Peilin, deputy general manager of Duntai Electronics Marketing (Figure 1), said that the rapid evolution of smartphones to mid-to-low prices has led Chinese mainland mobile phone manufacturers to expand the use of lower cost SITO touch panels to create more price competition Product. This will greatly increase the market penetration of the SITO solution, eroding the current market share of mainstream DITO (Double ITO). Including SITO double glass (G / G), single glass (OGS) with glass as the main sensing layer, and SITO single film (G / F) in the thin film technology camp (Figure 2) will be large Fat City.
Figure 1 Bai Peilin, deputy general manager of Duntai Electronics Marketing, mentioned that for the touch panel of more than 5 inches, the industry is currently optimistic about the development potential of OGS, and chip manufacturers and touch module factories are committed to developing related solutions.
Bai Peilin pointed out that based on the current order demand of mobile device brand manufacturers and the stock situation of touch chip and module factories, this year's SITO solution will account for 70% of the overall market shipments, gaining a dominant position in mobile touch technology.
As the name suggests, SITO uses a single layer of ITO to sense touch signals. It places the X and Y axis sensing wires on the same layer of ITO, and then it is laminated with a glass substrate or polyester film (PET) to form a touch panel; In the traditional DITO technology using double-layer ITO, SITO can reduce the ITO alignment, bonding process and material cost. The manufacturing process is relatively simple, which can meet the conditions of the BOM cost limit and rapid listing of low-cost smartphones. . However, SITO concentrates the sensing line on one layer, which will cause the problem that the capacitance value is too large to reduce the accuracy, and the greatly simplified panel structure will also reduce the strength, which is a technical barrier that needs to be overcome at present.
Figure 2 Comparison of various touch solutions
At this stage, touch chip manufacturers and module manufacturers are keeping up with the market pulse, and are fully committed to the development of a new generation of SITO products, and actively improve the yield and reliability, in the hope of winning more mobile phone manufacturers. Bai Peilin revealed that almost all mobile phone manufacturers in mainland China will focus on the low-end market this year. Because product price considerations are better than performance and stability requirements, and the screen size is mostly set below 5 inches, there is no need to support multi-touch; therefore, Tun Thai has tailored a variety of low-cost SITO touch-sensing chips, including single-layer self-capacitance true two-point sensing, single-layer self-capacitance two-finger gesture sensing, and single-layer mutual capacitance multi-point sensing, etc., to fully attract mobile phone manufacturers.
On the other hand, the In-cell touch panel solution, which has attracted the attention of the industry, is expected to break through the shackles of mass production in the second half of this year, further expanding its influence in the high-end smartphone market.
In-cell sensing structure renovation mass production yield / reliability surge
In the current small and medium size touch solutions, mass production yield and capacity have reached a certain level of GG, double film (GFF), OGS or On-cell, the thickness is mostly between 2.1? 3.0 millimeters (mm), which is not as good In-cell can achieve the ultimate thin and light performance of 1.8 mm; and this difference of a few centimetres is the most important competition for mobile phone manufacturers, including Apple, Sony, and even mainland Chinese brand players have all invested in the layout. , Thus making In-cell the focus of the touch industry.
However, In-cell built the touch-sensing layer in the liquid crystal display (LCD) panel, which not only increases the production difficulty, damage rate and liquid crystal noise problems, but also the sensing accuracy and stability are not in place; in the whole In the case of low yield and shortage of production capacity, the price is also expensive.
Bai Peilin revealed that in order to overcome the severe challenges of In-cell and speed up the listing and price reduction of terminal products, Duntai has developed a new generation of In-cell touch panel patents, which can increase the yield to general glass and thin film touch solutions. Quite a bit. This innovative structure improves Apple's In-cell method, turning the sensing layer from the bottom to the top of the LCD (Figure 3), which can shorten the distance between the finger and the sensing layer and avoid serious noise interference from the liquid crystal layer .
Figure 3 Comparison of existing In-cell technology architectures. Apple patents on the left and Duntai patents on the right.
Although Duntai's approach is expected to overcome the biggest bottleneck of In-cell mass production, the design space above the LCD is tighter than below, and the distance between the X and Y sensing layers will be shortened, which will amplify the capacitance of the two poles and affect the touch signal. Identification and sensing accuracy. Focusing on this, Duntai will also combine its own touch IC hardware and software, and the silicon intellectual property (IP) technology of the LCD driver IC supply chain under the cooperative panel factory, and will release an integrated system on a chip (SoC) in the second half of this year. ) To enhance the synchronization or time-sharing processing capabilities of touch and LCD signals, so that the new In-cell sensing structure works without hindrance.
Bai Peilin revealed that Duntai has set a schedule for mass production of new In-cell touch panels with a number of mainland Chinese panel makers, and is continuing to discuss cooperation with Taiwan panel makers. Initially, it will lock in the mainstream specifications of 4-5 inch smartphones , After the second quarter of this year, quarter by quarter volume, to assist mobile phone manufacturers to create affordable high-standard In-cell products.
It is reported that in addition to mainland China's Huawei, ZTE and other first-line brand factories have planned to introduce In-cell touch solutions in new products, Coolpad will also launch a 6.5 mm In-cell smart type that is known as the world's thinnest in the second half of this year. Mobile phones show that the demand for In-cell's production capacity will be increasing.
The benefits of In-cell are well-known. Once more excellent sensing structures and touch chips are in place in the second half of the year, they will gradually exert the economic benefits of mass production, quickly enter the mainstream status of small and medium-sized touch, and set off a new wave of technology conversion.
Mobile phone size / price multiple touch solutions need to go hand in hand
Although In-cell is expected to gradually take advantage of the thin and light advantage to capture the high-end mobile phone market, but as mobile phone manufacturers are competing to develop 5? It has successfully mass-produced touch panels of more than 5 inches, and the higher the pixels, the more difficult it is to improve the yield of In-cell technology.
NPD DisplaySearch research director Xie Zhongli said that except for Apple, almost all other smartphone manufacturers regard Phablet as the main product, thus driving the touch technology of mobile phones to move toward the large size.
Because the larger-sized In-cell technology has not yet matured, and the cost is still much higher than other technologies; therefore, to accelerate the expansion of the Phablet lineup, mobile device brand manufacturers will consider applying other touch technologies, including On-cell , Ultra-thin GFF will become the focus of the manufacturer's layout, and even began to appear in the existing 7-inch tablet mainstream OGS (Nexus 7), GF2 (GF DITO) (iPad mini) and other sound waves.
In addition, as mainland Chinese mobile phone factories strive to build low- and mid-priced smartphones, touch module factories will continue to increase GF1 (GF SITO) and GF â–³ (GF Triangle) in order to reduce the cost of ITO materials and provide customers with cheaper quotations. ) The proportion of investment in products such as thin film touch technology.
Xie Zhongli analyzed that because the two emerging touch panel solutions only use one ITO film, the material cost can be greatly reduced, and the former can realize multi-touch, and the latter can also support two-point touch with gesture simulation. Controls are all in line with the needs of general smart phones, and will quickly rise in the market with the advantage of low module cost.
Xie Zhongli believes that due to the increasingly diversified size and market price distribution of smartphones, manufacturers must also select appropriate touch panel technology according to product specifications. This will enable various glasses, films, OGS or On-cell, In -cell touch solutions have emerged in the field of terminal product design at different price points, promoting the continuous rise of the output value of the entire touch industry.
According to NPD DisplaySearch survey statistics, the global output value of touch panels has reached about 16 billion US dollars in 2012. It is estimated that by 2018, the output value will be doubled to 31.9 billion US dollars, indicating strong market demand.
Wire Carrier & Tubular Carriers
Fabricated steel wire baskets and wire carriers are designed and manufactured using high quality steel tubing as well as sheet metal for the coiling of wire. A solid basket is often used in house for rod break-down and then used subsequently in wire drawing of large stranders for power cables. Wire carriers are used for coiling and packaging wire from wire drawing equipment, and are then used as in-house or shipping packages.
Wire Coiling Baskets
- Manufactured from high quality tubing
- Heavy duty construction
- Heavy duty construction
- Various sizes per application
- Standard sizes per coiler
- Manufactured from high quality tubing
- Light-to-heavy duty constructions
- Square, clover & star base
- Sizes as per request
Wire Carrier
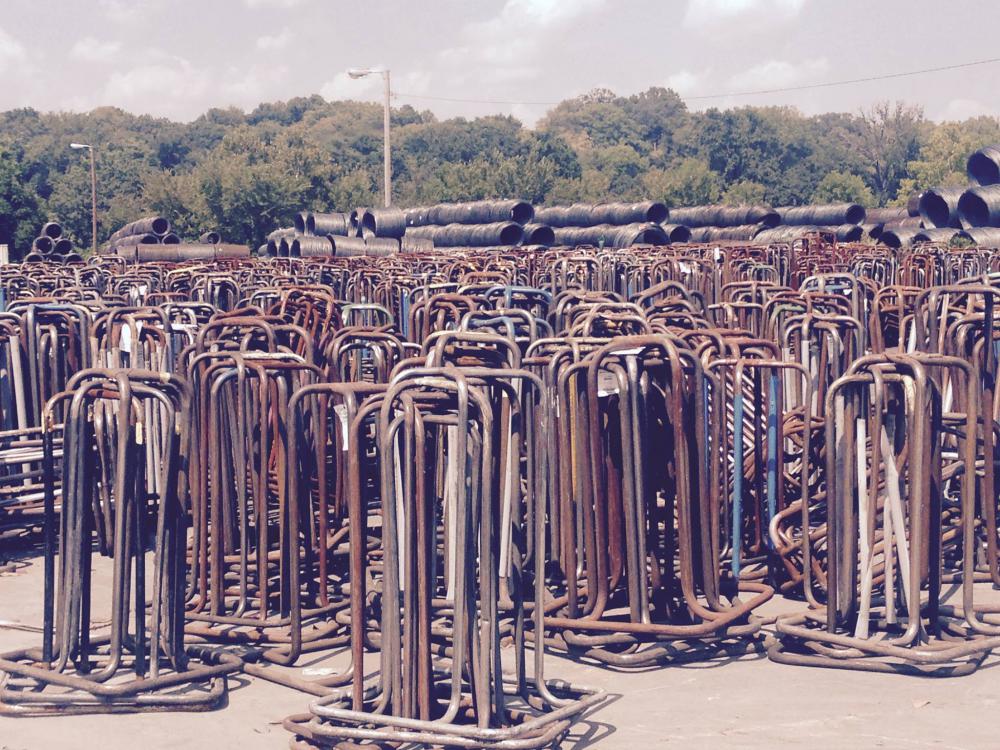
Wire Carrier
Coil Carriers, Cable Basket, Steel Basket, Steel Coiler, Wire Carrier
NINGBO BEILUN TIAOYUE MACHINE CO., LTD. , https://www.spool-manufacturer.com